Ultimate Guide to Preventing Weld Undercut: Tips and Techniques
Mastering the Art of Welding: Exactly How to Stay Clear Of Undercut Welding Issues for Flawless Construction Outcomes
Efficiency and accuracy are critical in the globe of welding, where even the smallest blemish can compromise the architectural integrity of a produced item. One common obstacle that welders face is damaging, a flaw that can deteriorate a weld joint and lead to expensive rework. By understanding the origin creates of undercut welding and implementing efficient techniques to stop it, welders can elevate their craft to new levels of excellence (Preventing weld undercut). In the quest of remarkable manufacture outcomes, understanding the art of welding to stay clear of undercut problems is not just a skill however a need for those making every effort for excellence in their job.
Understanding Undercut Welding
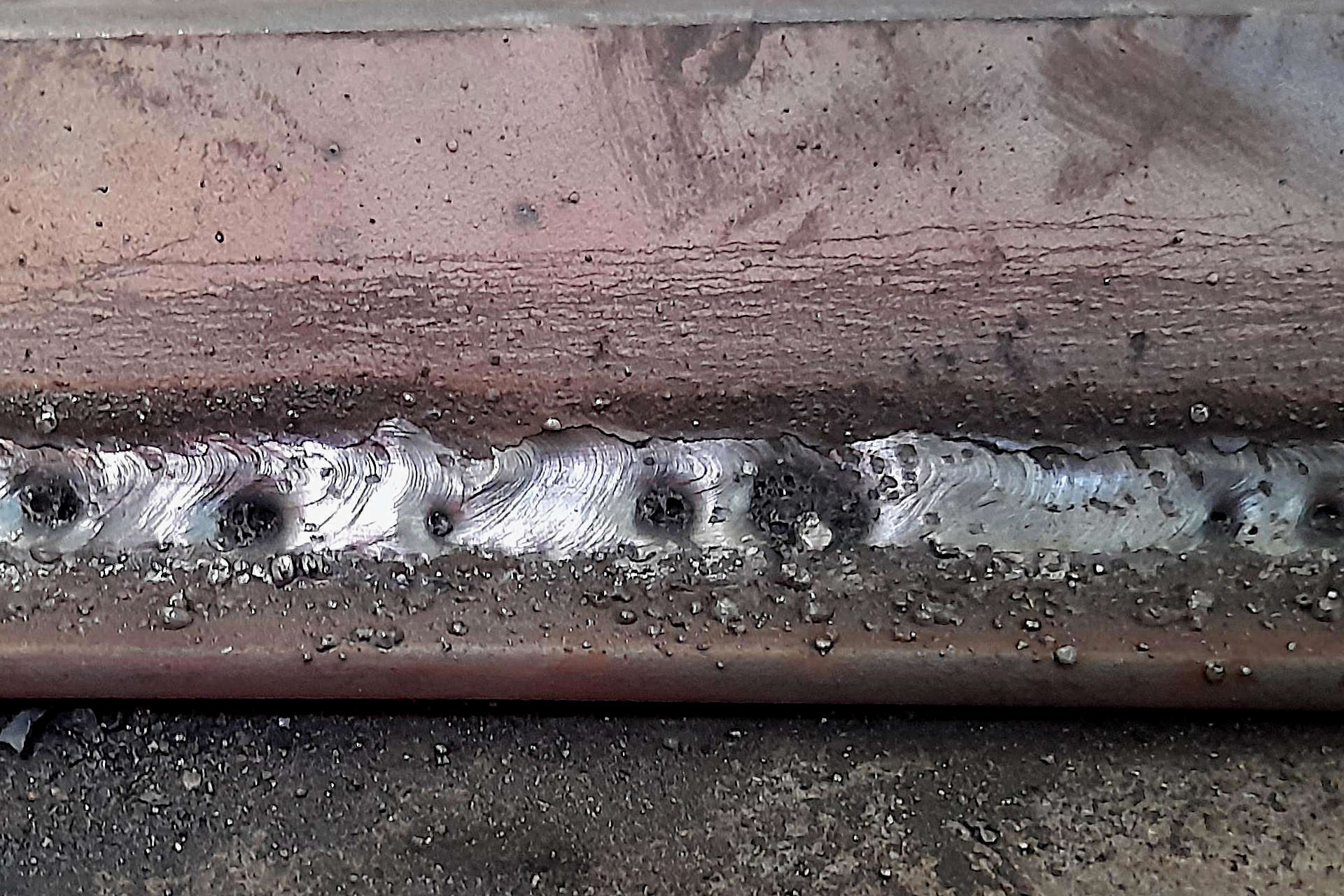
To protect against undercut welding, welders must ensure correct welding criteria, such as readjusting the current, voltage, traveling speed, and maintaining the proper electrode angle. By recognizing the causes of undercut welding and implementing preventative actions, welders can accomplish high-grade, structurally audio welds.
Reasons of Undercut in Welding
Recognizing the factors that add to damage in welding is important for welders to generate top notch, structurally sound welds. Insufficient welding existing or incorrect welding speed can likewise add to damage. Understanding these reasons and executing correct welding techniques can help stop damaging problems, ensuring sturdy and strong welds.
Techniques to stop Undercutting

To reduce the danger of undercutting in welding, welders can employ tactical welding techniques aimed at boosting the quality and integrity of the weld joints. Additionally, using the correct welding strategy for the certain joint configuration, such as weave or stringer grains, can add to minimizing undercutting.
Additionally, proper joint prep work, including ensuring tidy base products free of contaminants and making use of the suitable welding consumables, is vital in avoiding undercut issues. Utilizing back-step welding strategies and managing the weld bead account can additionally aid distribute warm evenly and minimize the threat of undercut. Normal examination of the weld joint throughout and after welding, as well as implementing top quality guarantee actions, can help in identifying and attending to damaging issues without delay. By carrying out these techniques faithfully, welders can accomplish remarkable construction results with marginal undercut issues.
Relevance of Correct Welding Parameters
Choosing and keeping appropriate welding specifications is crucial for attaining successful welds with marginal problems. Welding criteria describe variables such as voltage, existing, travel rate, electrode angle, and securing gas circulation price that directly impact the welding Go Here procedure. These parameters should be very carefully readjusted based upon the kind of product being welded, its thickness, and the welding strategy employed.
Proper welding specifications guarantee the best news quantity of warmth is applied to thaw the base steels and filler product consistently. If the specifications are established as well high, it can lead to extreme warmth input, creating burn-through, spatter, or distortion. On the other hand, if the parameters are also low, incomplete fusion, absence of infiltration, or damaging may happen.
Top Quality Guarantee in Welding Operations

Verdict
To conclude, grasping the art of welding calls for a comprehensive understanding of undercut welding, its causes, and techniques to prevent it. By making certain proper welding criteria and executing quality guarantee practices, flawless construction outcomes can be achieved. It is crucial for welders to regularly aim for quality in their welding operations to avoid undercut problems and generate high-grade welds.
Undercut welding, a common problem in welding processes, takes place when the weld metal does not appropriately load the groove and leaves a groove or clinical depression along the welded joint.To prevent undercut welding, welders must guarantee appropriate welding specifications, such as readjusting the existing, voltage, traveling rate, and preserving the right electrode angle. Inadequate welding incorrect or existing welding speed can additionally add to damage.To alleviate the threat of damaging in welding, welders can employ strategic welding strategies intended at improving the high quality and stability of the weld joints.In conclusion, mastering the art of welding needs a detailed understanding of undercut welding, its causes, and methods to avoid it.